Custom-Made Sprockets
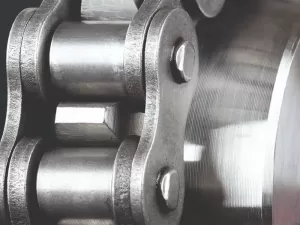
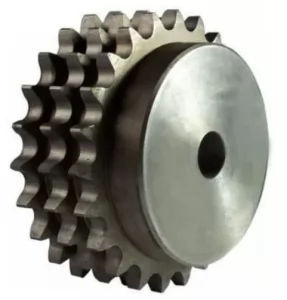
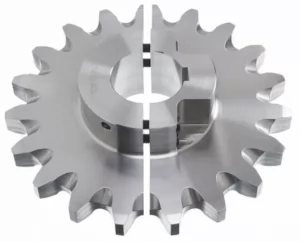
What is Chain Sprocket?
Sprocket and chain kits are gears with teeth which lock onto a chain. When the it rotates, the teeth hold the chain and drive the chain together with the other parts attached to it. This operation provides a controlled rotational movement of large equipment and machinery.It is manufactured from metal or reinforced plastic to handle the force of a moving chain.
They make direct contact with a variety of chain rings unlike gears which interlock together to transfer rotational movement. They are distinguished from a gear in that sprockets are never meshed together directly
They are parts that are made with specific chain rings to correctly fit and handle specific loads. They need to meet tight specifications regarding factors such as:
- Size
- Dimensionsli>
- Diameter
- Teeth width and depth
Choosing the proper gear is crucial because it can cause you heavy loss when using a wrong product where the teeth would chip or break. On the other hand, a sprocket with the correct chain can move without breaking, even in heavy-duty conveyor system applications.
They are used in bicycles, motorcycles, tracked vehicles, and other machinery either to transmit rotary motion between two shafts where gears are unsuitable or to impart linear motion to a track, tape etc.
Chain sprocket is used for power transmission from one shaft to another where slippage is not admissible, so they are being used instead of belts or ropes and sprocket-wheels instead of pulleys. They can be run at high speed and some forms of chain are so constructed as to be noiseless even at high speed.
Industrial Chain Sprockets are used mainly for the following applications ;
- Agricultural and farming equipment
- Automotive equipment
- Chain-driven machinery, such as conveyor belts and other factory systems
- Pulleys, shafts, and other power transmission equipment
- Vehicles, such as bicycles and motorcycles
The types of sprockets:
Different types of sprockets have different hubs. A hub is the added thickness around the central plate of a sprocket that doesn’t include the teeth. There are four main types of link chain sprockets as established by the ANSI:
The different types allow for different applications. Thus, chain and sprocket must be suitable for each other. Type A and B ones fit easily against Equipment with tolerance, while Type C ones are generally larger and need more thickness to support weight.
System performance highly depends on sprocket and chain interaction, which means your choice of sprockets can elevate your operation’s success. As Makelsan Chain we provide the right type of product that corresponds with the matching chain.
There are many design range of chain and sprocket kit:
- in single and double sided hub design
- divided sprockets
- sprockets with bolted-on segments or tooth shells
- shear-pin sprockets
These are the most common types. They work only with chains designed by rollers interconnected by pins. As Makelsan, we are one of the large chain sprocket suppliers.
Roller chains provide a gap that fits the teeth of the sprocket to transfer rotary motion. These are used in transmission equipment applications.
The performance of a conveyor chain sprocket or drive depends on sprocket-chain interaction. Using the right product is just as important as choosing the right chain.
Large sprocket and chains are a decisive factor in the capability and service life of every chain system. We therefore produce our own sprockets to ensure the high quality of all products.
We supply the corresponding products for all chains. We produce in high quality materials with tempered and additionally inductively hardened teeth.
What Purpose Does Chain Sprocket Serve?
Transmitting power, conveying materials, and timing purposes are the three fundamental purposes of chain sprockets. Moreover, chain and sprockets are the indespensable components of power transmission. These components convey speed and torque effectively by using a connected chain and sprockets. This combination ensures a consistent speed ratio, making them really suitable for such applications.
Where Are Chain Sprockets Used?
Chain sprockets are utilized in a variety of mechanical systems where precise motion and power transmission are important. They are generally found in bicycles and motorcycles, where they transfer power from the engine to the wheels, creating motion. In industrial areas, chain sprockets are essential in conveyor systems, used for material handling via manufacturing or processing plants. They are also common in agricultural machinery, heavy machinery, and automotive timing systems where they enable efficient transfer of power and motion between machine parts.
Makelsan Sprocket and Chain Production
Makelsan Chain, a Custom Sprocket Manufacturer, excels in specializing industrial sprockets and gears & chain sprocket guard, generally used for efficient power transfer in many industries. Our expertise spans from our carefully manufactured sprockets, crafted from high-quality materials, ensuring durability and longevity. Using advanced technologies, Makelsan Chain manufactures a wide range of customized sprockets tailored to your specific needs, from various types, dimensions, and sizes.
Makelsan sprockets are carefully manufactured from materials like stainless steel for high-temperature resistance, cast iron to be used in conveyor belts, and reinforced plastics for durability in extreme conditions. The reason why our sprockets are robust is that we utilize advanced gear manufacturing techniques. Our broaching machines are used to meticulously create teeth on each sprocket, ensuring that they can remain strong even in extreme situations. For this reason, our dedication to quality is shown by precise steps like drilling, heat treatment, and manual finishing to reach the highest standards in our products.
What are the Advantages of Using Chain Sprockets?
In industrial applications, chain sprockets offer many advantages for power transmission systems. One of their best benefits is the ability to transmit high torque which is important in heavy-duty machinery. Ensuring synchronized and smooth operation, they provide a reliable and constant speed where systems like conveyor belts need. Chain sprockets are durable and require low maintenance so that they can withstand harsh conditions.
How is the Maintenance of Chain Sprockets Conducted?
To ensure their longevity and performance, chain sprockets have a series of regular checks. First of all, it's significant to inspect the chain and sprockets routinely for any kind of wear or any potential misalignments. Lubrication plays an important role in maintenance because applying appropriate lubricants lessens wear, and extends the lifespan of both the chain and sprockets. Moreover, they should be kept clean as dirt may cause some kind of premature wear.
You can have information about Makelsan chain and link chain supply processes and examine industrial chain types
Chain Sprocket Size Chart
No of teeth
(Z) |
8.00 | 3/8
9.53 |
1/2
12.70 |
5/8
15.88 |
3/4
19.05 |
1
25.40 |
1 1/4
31.75 |
1 1/2
38.10 |
13/4
44.45 |
2
50.80 |
2 1/2
63.50 |
3
76.20 |
3 1/2
88.90 |
4
101.60 |
9 | 28.7 | 33.5 | 44.5 | 56.4 | 68.1 | 90.9 | 114.8 | 133.9 | 158.8 | 186.0 | 227.9 | 271.8 | 320.8 | 363.7 |
10 | 30.7 | 35.8 | 47.8 | 60.5 | 72.9 | 97.6 | 123.2 | 143.8 | 170.5 | 199.2 | 244.4 | 291.6 | 343.9 | 389.9 |
11 | 32.8 | 38.6 | 51.3 | 64.8 | 78.0 | 104.4 | 131.9 | 154.0 | 182.4 | 212.9 | 261.4 | 312.2 | 367.8 | 417.3 |
12 | 35.1 | 41.2 | 54.9 | 69.4 | 83.3 | 111.5 | 140.5 | 164.6 | 194.8 | 226.8 | 279.2 | 333.3 | 392.4 | 445.8 |
13 | 38.4 | 45.0 | 60.0 | 75.5 | 91.0 | 124.4 | 152.9 | 180.1 | 212.4 | 246.2 | 304.1 | 363.5 | 427.2 | 485.7 |
14 | 40.7 | 47.8 | 63.8 | 80.3 | 96.5 | 129.1 | 162.3 | 191.3 | 225.3 | 261.1 | 322.6 | 385.8 | 453.4 | 515.6 |
15 | 43.0 | 50.6 | 67.6 | 84.9 | 102.1 | 136.4 | 171.7 | 202.7 | 238.8 | 276.4 | 341.6 | 408.7 | 479.8 | 545.9 |
16 | 45.5 | 53.6 | 71.4 | 89.7 | 108.0 | 144.0 | 181.1 | 214.2 | 252.0 | 291.6 | 360.7 | 431.6 | 506.5 | 576.3 |
17 | 47.8 | 56.4 | 75.2 | 94.5 | 113.6 | 151.9 | 190.8 | 225.6 | 265.5 | 306.9 | 379.7 | 454.4 | 533.4 | 607.1 |
18 | 50.3 | 59.2 | 79.0 | 99.3 | 119.4 | 159.5 | 200.4 | 237.3 | 278.9 | 322.4 | 399.3 | 477.8 | 560.3 | 638.1 |
19 | 52.6 | 62.2 | 82.8 | 104.2 | 125.2 | 167.4 | 210.1 | 248.7 | 292.6 | 337.9 | 418.6 | 500.9 | 587.5 | 669.1 |
20 | 55.9 | 66.3 | 88.4 | 110.8 | 133.1 | 177.8 | 222.8 | 265.0 | 310.7 | 356.9 | 444.3 | 532.4 | 622.8 | 610.5 |
21 | 58.4 | 69.1 | 92.2 | 115.8 | 139.2 | 185.7 | 232.4 | 276.6 | 324.4 | 372.6 | 464.1 | 556.0 | 650.5 | 742.0 |
22 | 61.0 | 72.2 | 96.3 | 120.7 | 145.1 | 193.6 | 242.3 | 288.6 | 338.4 | 388.6 | 483.8 | 579.7 | 678.2 | 773.5 |
23 | 63.5 | 75.2 | 100.1 | 125.8 | 150.9 | 201.4 | 252.2 | 300.3 | 352.1 | 404.4 | 503.7 | 603.3 | 705.9 | 805.2 |
24 | 65.8 | 78.3 | 104.2 | 130.6 | 157.0 | 209.3 | 262.2 | 312.2 | 366.0 | 420.2 | 523.5 | 627.1 | 733.6 | 837.0 |
25 | 68.4 | 81.0 | 108.2 | 135.7 | 162.8 | 217.4 | 272.1 | 324.1 | 380.0 | 436.2 | 543.3 | 651.0 | 761.5 | 868.7 |
26 | 70.9 | 84.1 | 112.0 | 140.5 | 168.9 | 225.3 | 282.0 | 336.1 | 393.7 | 451.9 | 563.1 | 674.9 | 789.2 | 900.5 |
27 | 73.4 | 86.9 | 115.8 | 145.6 | 174.8 | 233.2 | 292.1 | 347.8 | 407.7 | 468.4 | 583.2 | 698.8 | 817.4 | 932.5 |
28 | 76.0 | 89.9 | 119.9 | 150.4 | 180.9 | 241.3 | 302.0 | 359.7 | 421.7 | 484.1 | 603.3 | 722.7 | 845.3 | 964.2 |
29 | 78.5 | 93.0 | 124.0 | 155.5 | 186.7 | 249.2 | 312.2 | 371.6 | 435.6 | 500.1 | 623.1 | 746.5 | 873.3 | 996.2 |
30 | 81.0 | 96.0 | 127.8 | 160.6 | 192.8 | 257.3 | 322.1 | 383.8 | 449.6 | 516.1 | 643.2 | 770.4 | 901.2 | 1028.2 |
31 | 83.6 | 99.1 | 131.9 | 165.4 | 198.6 | 265.2 | 332.0 | 395.8 | 463.6 | 532.1 | 663.0 | 794.5 | 929.1 | 1060.2 |
32 | 86.1 | 101.9 | 135.9 | 170.5 | 204.7 | 273.3 | 342.2 | 407.7 | 477.6 | 548.1 | 683.0 | 818.4 | 957.1 | 1092.2 |
33 | 88.4 | 104.9 | 140.0 | 175.5 | 210.8 | 281.2 | 352.1 | 419.6 | 491.8 | 564.1 | 703.1 | 842.5 | 985.3 | 1124.2 |
34 | 91.0 | 108.0 | 143.8 | 180.4 | 216.7 | 289.3 | 362.0 | 431.8 | 505.7 | 580.2 | 723.2 | 866.4 | 1013.2 | 1156.2 |
35 | 93.5 | 111.0 | 147.9 | 185.4 | 222.8 | 297.2 | 372.1 | 443.8 | 519.7 | 596.2 | 743.2 | 890.5 | 1041.2 | 1188.2 |
36 | 96.0 | 114.1 | 151.9 | 190.5 | 228.9 | 305.3 | 382.0 | 455.8 | 533.7 | 612.2 | 763.0 | 914.7 | 1069.4 | 1220.2 |
37 | 98.6 | 116.9 | 156.0 | 195.6 | 234.7 | 313.2 | 392.2 | 467.9 | 547.7 | 628.4 | 783.1 | 938.8 | 1097.3 | 1252.5 |
38 | 101.1 | 119.9 | 160.0 | 200.4 | 240.8 | 321.3 | 402.1 | 479.8 | 561.9 | 644.4 | 803.2 | 962.7 | 1125.5 | 1284.5 |
39 | 103.7 | 123.0 | 163.8 | 205.5 | 246.9 | 329.2 | 412.3 | 491.8 | 575.9 | 660.4 | 823.2 | 986.8 | 1153.7 | 1316.5 |
40 | 106.2 | 126.0 | 167.9 | 210.6 | 252.8 | 337.3 | 422.4 | 503.7 | 589.8 | 676.9 | 843.5 | 1010.9 | 1181.9 | 1348.8 |
41 | 108.7 | 129.0 | 172.0 | 215.4 | 258.9 | 345.5 | 432.3 | 515.6 | 604.0 | 692.9 | 863.6 | 1035.1 | 1210.1 | 1381.0 |
42 | 111.3 | 132.1 | 175.8 | 220.5 | 264.9 | 353.3 | 442.5 | 527.8 | 618.0 | 708.9 | 883.7 | 1059.2 | 1238.3 | 1413.0 |
43 | 113.8 | 134.9 | 179.8 | 225.6 | 270.8 | 361.5 | 452.4 | 539.8 | 632.2 | 725.2 | 903.8 | 1083.3 | 1266.5 | 1445.3 |
44 | 116.4 | 138.0 | 183.9 | 230.7 | 276.9 | 369.6 | 462.6 | 552.0 | 646.2 | 741.2 | 923.8 | 1107.5 | 1294.4 | 1447.3 |
45 | 118.9 | 141.0 | 188.0 | 235.7 | 283.0 | 377.5 | 472.7 | 563.9 | 660.2 | 757.2 | 943.8 | 1131.6 | 1322.6 | 1509.5 |
46 | 121.4 | 144.0 | 192.0 | 240.6 | 289.1 | 385.6 | 486.6 | 576.1 | 674.4 | 773.5 | 964.2 | 1155.7 | 1350.8 | 1540.5 |
47 | 124.0 | 147.1 | 196.1 | 245.6 | 294.9 | 393.7 | 492.8 | 588.0 | 688.4 | 789.5 | 984.3 | 1179.9 | 1379.0 | 1572.8 |
48 | 126.5 | 150.1 | 199.9 | 250.7 | 301.0 | 401.6 | 502.7 | 600.2 | 702.6 | 805.5 | 1004.3 | 1204.0 | 1407.2 | 1605.3 |
49 | 129.1 | 153.2 | 204.0 | 255.8 | 307.1 | 409.7 | 512.8 | 612.2 | 716.6 | 821.7 | 1024.4 | 1228.1 | 1435.4 | 1637.6 |
50 | 131.6 | 156.2 | 208.0 | 260.9 | 313.2 | 417.9 | 532.0 | 624.3 | 730.8 | 837.7 | 1044.5 | 1252.2 | 1463.6 | 1669.8 |
51 | 134.1 | 159.0 | 212.1 | 265.7 | 319.0 | 425.7 | 532.9 | 636.3 | 744.8 | 853.7 | 1064.8 | 1276.4 | 1491.5 | 1702.1 |
52 | 136.7 | 162.1 | 216.2 | 270.8 | 325.1 | 433.9 | 543.1 | 648.5 | 758.7 | 870.0 | 1084.8 | 1300.5 | 1519.7 | 1734.6 |
53 | 139.2 | 165.1 | 220.2 | 275.9 | 331.2 | 442.0 | 553.2 | 660.4 | 773.0 | 886.0 | 1104.9 | 1324.6 | 1547.9 | 1766.8 |
54 | 141.8 | 168.2 | 224.3 | 280.9 | 337.3 | 450.1 | 563.2 | 672.6 | 786.9 | 902.2 | 1125.2 | 1348.8 | 1576.1 | 1799.1 |
55 | 144.3 | 171.2 | 228.1 | 286.0 | 343.4 | 458.0 | 573.3 | 684.6 | 801.2 | 918.2 | 1145.3 | 1372.9 | 1604.3 | 1831.4 |
56 | 146.8 | 174.3 | 232.2 | 290.9 | 349.3 | 466.1 | 583.2 | 696.7 | 815.1 | 934.5 | 1165.4 | 1397.3 | 1632.5 | 1863.9 |
57 | 149.4 | 177.3 | 236.2 | 295.9 | 355.4 | 474.2 | 593.4 | 708.9 | 829.3 | 950.5 | 1185.4 | 1412.4 | 1660.9 | 1896.1 |
58 | 152.0 | 180.4 | 240.3 | 301.0 | 361.5 | 482.1 | 603.5 | 720.9 | 843.6 | 966.5 | 1205.8 | 1445.5 | 1689.1 | 1928.3 |
59 | 145.4 | 183.4 | 244.4 | 306.1 | 367.6 | 490.2 | 613.4 | 733.1 | 857.6 | 982.7 | 1225.8 | 1469.7 | 1717.3 | 1960.6 |
60 | 157.0 | 186.2 | 284.4 | 311.2 | 373.7 | 498.4 | 623.6 | 745.0 | 871.7 | 998.7 | 1245.9 | 1493.8 | 1745.5 | 1993.2 |
61 | 159.5 | 189.3 | 252.5 | 316.3 | 379.5 | 506.5 | 633.8 | 557.2 | 885.7 | 1015.0 | 1266.2 | 1518.2 | 1773.7 | 2025.4 |
62 | 162.1 | 192.3 | 256.3 | 321.1 | 385.6 | 514.4 | 643.7 | 769.4 | 899.9 | 1031.0 | 1286.3 | 1542.3 | 1801.9 | 2057.7 |
63 | 164.6 | 195.4 | 260.4 | 326.2 | 391.7 | 522.5 | 653.8 | 781.3 | 913.9 | 1047.3 | 1306.3 | 1566.4 | 1830.1 | 2089.4 |
64 | 167.2 | 198.4 | 264.4 | 331.2 | 397.8 | 530.6 | 664.0 | 793.5 | 928.2 | 1063.3 | 1326.7 | 1590.6 | 1858.3 | 2121.7 |
65 | 169.7 | 201.4 | 268.5 | 336.3 | 403.9 | 538.7 | 674.1 | 805..7 | 942.1 | 1079.5 | 1346.7 | 1615.0 | 1886.5 | 2153.9 |
66 | 172.2 | 204.5 | 272.6 | 341.4 | 409.7 | 546.6 | 684.0 | 817.6 | 956.3 | 1095.5 | 1367.1 | 1639.1 | 1914.7 | 2186.2 |
67 | 174.8 | 207.5 | 276.6 | 346.5 | 415.8 | 554.8 | 694.2 | 829.8 | 970.6 | 1111.8 | 1387.1 | 1663.2 | 1943.1 | 2218.4 |
68 | 177.3 | 210.6 | 280.7 | 351.6 | 421.9 | 562.9 | 704.4 | 841.8 | 984.5 | 1127.8 | 1407.2 | 1687.3 | 1971.3 | 2050.7 |
69 | 179.9 | 213.6 | 284.8 | 356.5 | 428.0 | 571.0 | 714.3 | 854.0 | 998.8 | 1144.0 | 1427.5 | 1711.7 | 1999.5 | 2283.0 |
70 | 182.4 | 216.7 | 288.6 | 361.4 | 434.1 | 578.9 | 724.4 | 866.2 | 1012.7 | 1160.0 | 1447.6 | 1735.9 | 2027.7 | 2315.2 |
71 | 184.9 | 219.5 | 292.6 | 366.5 | 440.2 | 587.0 | 734.6 | 878.1 | 1026.9 | 1176.3 | 1467.9 | 1760.0 | 2055.9 | 2347.5 |
72 | 187.5 | 222.5 | 296.7 | 371.6 | 446.0 | 595.1 | 744.5 | 890.3 | 1040.9 | 1192.3 | 1487.9 | 1784.1 | 2084.1 | 2380.0 |
73 | 190.0 | 225.6 | 300.8 | 376.7 | 452.1 | 603.3 | 754.7 | 902.5 | 1055.2 | 1208.5 | 1508.0 | 1808.5 | 2112.5 | 2412.3 |
74 | 192.5 | 228.6 | 304.8 | 381.8 | 458.2 | 611.1 | 764.8 | 914.4 | 1069.4 | 1224.8 | 1528.3 | 1832.6 | 2140.7 | 2444.5 |
75 | 195.1 | 231.7 | 308.9 | 386.9 | 464.3 | 619.3 | 775.0 | 926.6 | 1083.3 | 1240.8 | 1548.4 | 1856.8 | 2168.9 | 2476.8 |
76 | 197.6 | 234.7 | 313.0 | 391.7 | 470.4 | 627.4 | 784.9 | 938.8 | 1097.5 | 1257.1 | 1568.7 | 1881.1 | 2197.1 | 2509.0 |
77 | 200.2 | 237.8 | 317.0 | 396.8 | 476.5 | 635.5 | 795.0 | 950.7 | 1111.5 | 1273.1 | 1588.8 | 1905.3 | 2225.3 | 2541.3 |
78 | 202.7 | 240.8 | 321.1 | 401.9 | 482.4 | 634.7 | 805.2 | 962.9 | 1125.8 | 1289.3 | 1609.1 | 1929.4 | 2253.8 | 2573.5 |
79 | 205.2 | 243.9 | 324.9 | 406.9 | 488.5 | 651.5 | 815.1 | 975.1 | 1140.0 | 1305.3 | 1629.2 | 1953.8 | 2282.0 | 2605.8 |
80 | 207.8 | 246.9 | 329.0 | 412.0 | 494.6 | 659.7 | 825.5 | 986.8 | 1154.0 | 1321.8 | 1649.5 | 1977.9 | 2310.4 | 2638.3 |
FAQ
The majority of conveyor chain manufacturers will state that the rate of elongation must not exceed 3%. If it is 3% or above, it is time to replace your roller chain.
If the roller chain has not been replaced, it can cause the chain to dislodge from the sprockets and cause a power transmission failure with broken links causing potential damage to other components of the product.
Check the adjusters on your swingarms. If you have maxed out the available adjustments , you should replace both your chain and sprockets. By pulling on the chain at the very rear of the sprocket, the sprocket teeth must stay inside of the chain links.
From where you would usually tension the chain, turn the wheel and check in several spots around the whole length for tight spots. If you find excessive tight areas where the tension differs significantly, you have stiff links. A thorough clean and re-lubrication can help.
Carefully examine your sprocket’s teeth the whole way around. Bear in mind that alloy sprockets will wear faster than those made of steel.
We advise replacing both the chain and sprockets at the same time to ensure both peace of mind and optimum performance delivery. It’s true that you don’t need to always replace them at the same time, however in our experience, it’s best to keep it simple and consistent.
An easy way to check for a worn chain is to try to pull the chain away from the rear of the sprocket on the rear wheel. If the chain is worn, you’ll reveal about half a tooth of the sprocket. A new chain will wrap around the sprocket snugly and won’t pull away.
Chain wear and stretch will cause grouping and excessive wear to the sprocket, a major cause of whipping. Poor Sprocket Alignment creates heat and may even bend the shafts on the drive system, causing great damage. Poor Pitch Integrity of chain and sprockets also causes premature failure.
- Chain size is commonly referred to as Pitch. In actuality, chain size is determined by the chain pitch. Pitch refers to the measurement from one roller-pin center to the next roller pin center of a given chain.
- ANSI (American National Standard Institute) chain pitch is always measured in 1/8” increments
If you have a sprocket and you need to measure the chain size, if you have just the sprocket, you can use calipers to measure between the teeth. Measure from center to center of where the chain roller would set between the teeth to find the measurement of the pitch. Once you know the pitch you can determine the chain size you need
- Following are the main types of sprockets:
- Chain sprockets
- Duplex sprockets
- Industrial sprockets
- Drive sprockets
- Triplex sprockets
- Shaft sprockets
- Simplex sprockets
- Single pitch and double pitch sprocket
- Drum sprockets
- Steel split sprockets
- Idler sprocket
- Bushed sprocket
- Multi-strand sprocket
- Quick disconnect sprocket
- Taper-lock sprocket
- Double plus sprocket
- Cast iron, which are mainly used in large gear ratios and heavy operating conditions. Cast Iron is the most common and economical material for flat wire belt sprockets, they are accurately cast from high grade iron. Other diameters can be provided on special order.
- Plastics – which are mainly used for low load conditions, depending on the design of sprocket as per the load conditions where in the lightweight gigs the maximum marks for in the use in idlers,wood processing machines,packaging machines , bottling machines etc. All plastic sprockets meet USDA and FDA for food contact.
-
- UHMW Polyethylene can withstand continuous temperatures up to 180 degrees F.
- High Temp UHMW Polyethylene can withstand continuous temperatures up to 220 degrees F.
- Nylon sprockets provide 2-3 times the strength of UHMW and can withstand higher temperatures.
- Steel alloys – used mainly for medium and heavy load applications. FL sprockets have no flange and a hub sticking out one side to allow debris to fall through the belt.
- Stainless Steels – Both Steel and SS falls in the medium and heavy load applications. Fully machined flangeless (-FL) or machined tooth (-MT) sprockets made from various stainless steels are also available.
The selection of material is purely depending on the loading conditions and gear ratios required. If the material has the attributes to fit your design then any material can be used. So the listed materials can be used or cannot be used. But these are some commonly used materials in the sprocket.